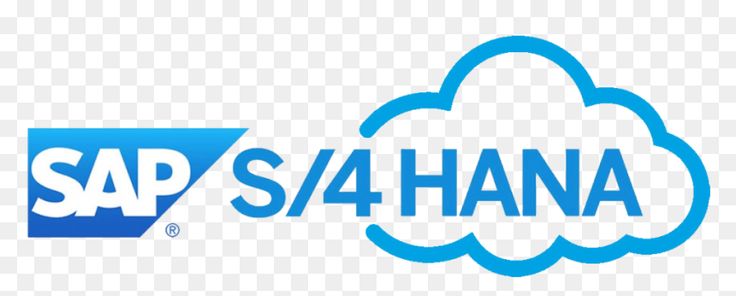
SAP S/4HANA Implementation
Implementing an ERP System for a Steel Manufacturing Company
Company Name: Alisha Steels.
Industry: Steel Manufacturing
Location: Global operations with headquarters in Bin Qasim, Pakistan.
Employees: 500+
Products: Steel Products
Alisha Steels. is a mid-sized company that designs, manufactures, and sells consumer electronics and home appliances. The company operates both online and offline retail channels, with manufacturing facilities in Asia and distribution centers in North America, Europe, and Asia.
Challenges Before ERP Implementation
- Disconnected Systems:
-
-
The company used multiple standalone systems for inventory management, manufacturing, sales, and accounting.
-
-
-
Data silos led to inefficiencies, errors, and delays in decision-making.
-
-
Inventory Management Issues:
-
-
Poor visibility into inventory levels across manufacturing facilities and retail stores.
-
-
-
Overstocking and stockouts were common, leading to lost sales and increased carrying costs.
-
-
Inefficient Manufacturing Processes:
-
- Lack of real-time data on production schedules, raw material availability, and machine utilization.
-
-
Delays in production due to poor coordination between departments.
-
- Customer Service Challenges:
-
-
Inaccurate order tracking and delayed deliveries due to manual processes.
-
-
-
Lack of integration between online and offline sales channels.
-
-
Financial Reporting Delays:
-
-
Manual consolidation of financial data from multiple systems resulted in delayed and inaccurate financial reports.
-
-
Scalability Issues:
-
-
Existing systems were not scalable to support the company’s growth plans, including expanding into new markets.
-
ERP Solution Selected
After evaluating several ERP vendors, Alisha Steels. selected SAP S/4HANA for its robust capabilities in retail and manufacturing, real-time data processing, and scalability.
Key Modules Implemented:
- Supply Chain Management (SCM):
- Integrated inventory management across manufacturing and retail.
- Demand forecasting and procurement planning.
- Manufacturing Execution System (MES):
- Real-time monitoring of production processes.
- Machine utilization tracking and maintenance scheduling.
- Sales and Distribution (SD):
- Unified sales order management for online and offline channels.
- Automated order tracking and delivery scheduling.
- Financial Accounting (FI) and Controlling (CO):
- Real-time financial reporting and consolidation.
- Cost tracking and profitability analysis.
- Customer Relationship Management (CRM):
- a. Centralized customer data for personalized marketing and support.
- b. Integration with sales and service teams.
- Human Capital Management (HCM):
- Employee management, payroll, and performance tracking.
Implementation Process
- Planning Phase (3 months):
- Conducted a needs assessment to identify key pain points and requirements.
- Formed a cross-functional implementation team, including IT, operations, finance, and HR.
- Defined project scope, timelines, and budget.
- Design Phase (4 months):
- Customized SAP S/4HANA modules to align with Stellar Goods’ business processes.
- Designed data migration strategy to transfer data from legacy systems.
- Conducted workshops with end-users to gather feedback and refine workflows.
- Development Phase (5 months):
- Configured the ERP system to meet business requirements.
- Developed custom reports and dashboards for real-time analytics.
- Integrated the ERP system with existing tools (e.g., e-commerce platforms, CRM).
- Testing Phase (2 months):
- Conducted unit testing, integration testing, and user acceptance testing (UAT).
- Resolved bugs and fine-tuned system performance.
- Deployment Phase (1 month):
- Rolled out the ERP system in phases, starting with manufacturing and retail operations.
- Provided training to employees on using the new system.
- Post-Implementation Support (Ongoing):
- Established a helpdesk for troubleshooting and support.
- Conducted regular system audits and updates
Results and Benefits
- Improved Inventory Management:
- Real-time visibility into inventory levels reduced overstocking.
- Optimized procurement processes led to a reduction in carrying costs.
- Enhanced Manufacturing Efficiency:
- Production delays decreased due to better coordination and realtime monitoring.
- Machine utilization improved increasing overall productivity.
- Streamlined Sales and Distribution:
- Order fulfillment time reduced improving customer satisfaction.
- Unified sales channels enabled seamless omnichannel experiences.
- Accurate Financial Reporting:
- Real-time financial data reduced month-end closing time from 10 days to 3 days.
- Improved cost tracking increased profitability.
- Scalability and Growth:
- The ERP system supported the company’s expansion into new markets, including Europe and Asia.
- Enabled the launch of new product lines without disrupting operations.
- Employee Productivity:
- Automated workflows reduced manual data entry, freeing up employees for higher-value tasks.
- Centralized data improved collaboration across departments.